Process Intensification and Continuous Reaction Technologies |
|
SBI Fine Chemicals Inc. is a pioneer in process intensification and continuous reaction processing and their applications. SBI’s proprietary Process Intensifying Continuous Flow-Through Reaction (PICFTR) reactor systems allow rapid scale up of routine and highly energetic reactions and the use of dangerous and sensitive chemicals, such as hydrazoic acid and organometallics, routinely and safely. |
|
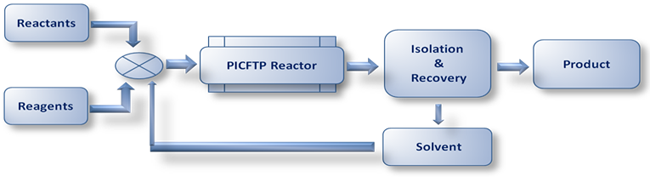 |
|
|
Fine chemical production, a critical stage of the pharmaceutical research, development, and manufacturing, typically occurs in a batch environment. A superior alternative production methodology known as continuous processing technologies can reduce operating expenses by 90% and capital expenses by 50%. |
|
SBI applies its revolutionary Process Intensifying Continuous Flow-Through Reaction (PICFTR) and Processing (PICFTP) technologies in the manufacturing of advanced pharmaceutical intermediates and fine chemicals. |
|
Specially Designed Modular PICFTR Reactor System: |
|
SBI's specially designed reactor system speeds up reactions by influencing reaction kinetics, thereby intensifying processing and reducing reaction times from hours to seconds. We design and develop special reactors and processing equipment to intensify reactions by influencing their reaction kinetics making them faster, safer, more consistent in quality, reproducibility and efficiency. |
|
Compared to traditional batch or continuous processing, SBI's PICFTR technologies have the following advantages: |
|
Improved Kinetics: Reduces reaction time from hours to seconds by influencing reaction kinetics. SBI's proprietary PICFTR reactor system, with superior mixing and heat exchange, intensifies the reaction. |
|
Handling of Energetic Exothermic Reactions: PICFTR can handle highly energetic reactions that are simply not possible on commercial scale in batch or even using other prevalent continuous processing technologies that are designed to accommodate only retention time. |
|
Improved Quality and Yield: PICFTR technology allows the performing of larger volume reactions by rapid cycling of minute batches with a high degree of accuracy and reproducibility. PICFTR technology enables precise control on process parameters in real time. This is a significant improvement over standard batch reactions, where process parameters are hard to control due to the large volumes involved. Due to this precise control, PICFTRs deliver more reproducible results than batch reactions. |
|
Ease of Scalability: PICFTR technology enables greater flexibility in production run sizes, which can be changed without making any modification in design or equipment size, thereby maintaining strict process parameters without compromising product quality or yields. Therefore, only the run time has to be increased, not the run size, to increase production scale. |
|
Improved Safety and Environmental Impact: With the reduction in quantities of reactants at any given moment to almost miniscule levels, various risks that affect the scalability of sensitive reactions are virtually eliminated. This, in turn, reduces the risk of accidents by almost eliminating the problems that are related to large scale batch reactions. |
|
Reduced Costs: PICFTR provides several-fold cost reduction compared with current manufacturing techniques due to lower initial capital expenditures, the increase in quality of output, and process automation. In particular, the superior performance of PICFTR technology allows operation at optimal reaction conditions, at higher concentrations or even solvent-less thereby minimizing raw materials wastage as well as the volumes of solvents and by-products that need to be handled or disposed of. Similarly, process automation results in increased efficiency and reduced labour costs. |
|
Reduced Energy Consumption: PICFTR technology can operate with highly concentrated reactants that reduce energy consumption by up to 30%. In contrast, batch production uses a large amount of solvent to dilute the reactants, consequently requiring energy demanding evaporation. |
|